If you’ve been following us on social media, you’ve probably seen some behind-the-scenes pictures of our new commercial project, 1 Lonsdale. Read on for details into the installation, and extension planning, of the mass timber structure.
Let’s start by introducing you to this project
1 Lonsdale is a three-storey, mass timber building set on a zero lot line in the heart of North Vancouver’s Shipyard District, and uniquely positioned at the very bottom of Lonsdale Ave.
The building’s ground floor, home to a new restaurant, has been designed to open onto Carrie Cates Court by incorporating floor-to-ceiling, Passive House certified, triple glazed windows and a south-facing exterior deck—that’s where you’ll find us come summer! The second and third level office spaces will feature exposed timber with unparalleled views of Lower Lonsdale.
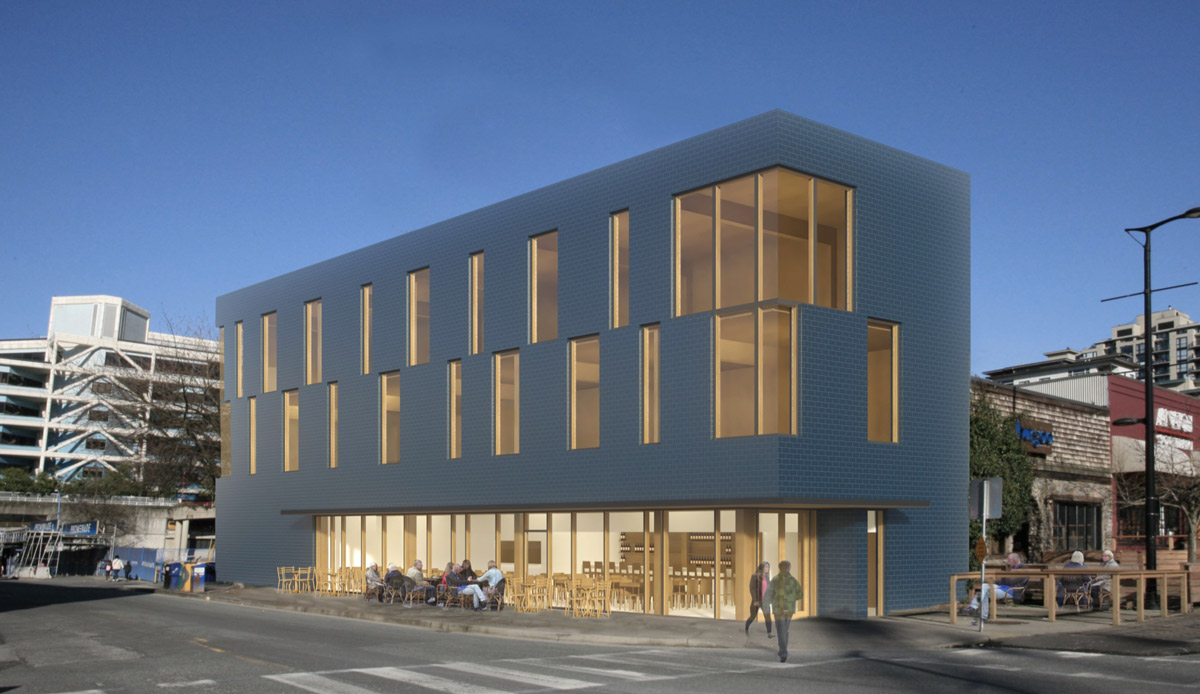
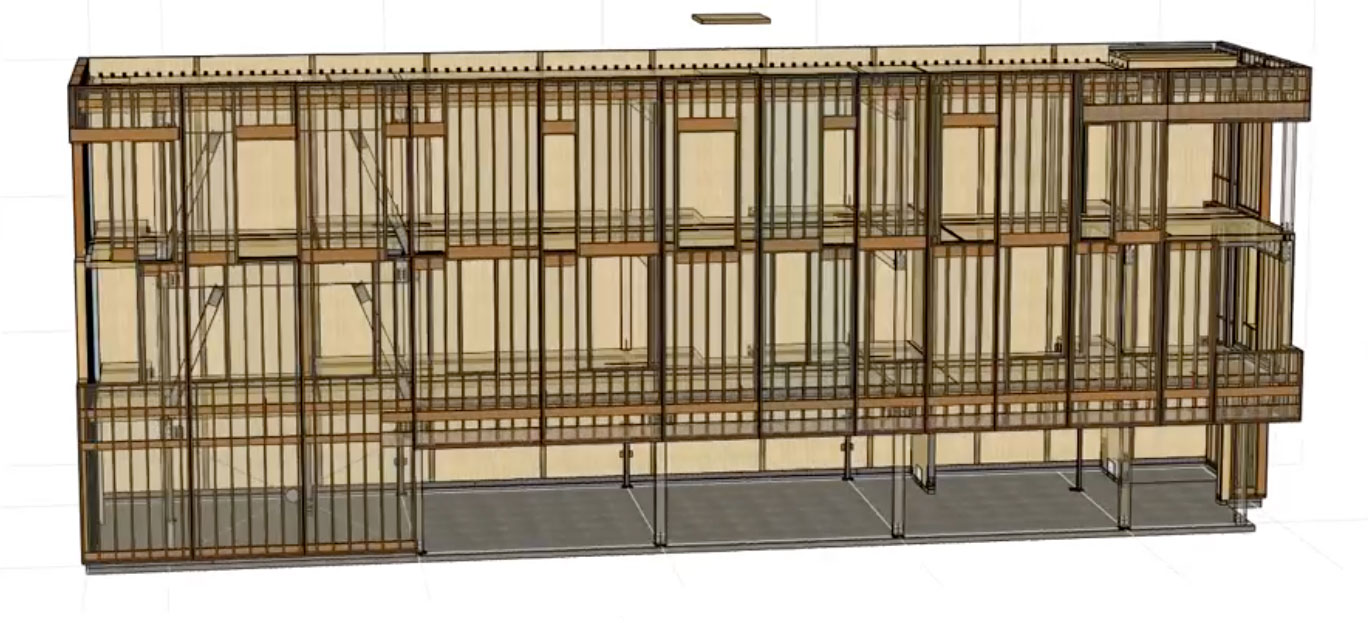
An image of the building model
How we built it
We always say one minute of planning saves ten in execution, and perhaps no project better exemplifies this ethos than 1 Lonsdale. We started planning installation months in advance when Senior Project Manager Brant built a virtual model of the project using Building Information Modeling (BIM).
Brant explains more in the video below:
With the digital model in place, it was time to assemble the crew to go through it in detail, before working on an erection plan for the mass timber elements. The structure consists of two primary products: Glulam and Cross-Laminated Timber (CLT) panelling.
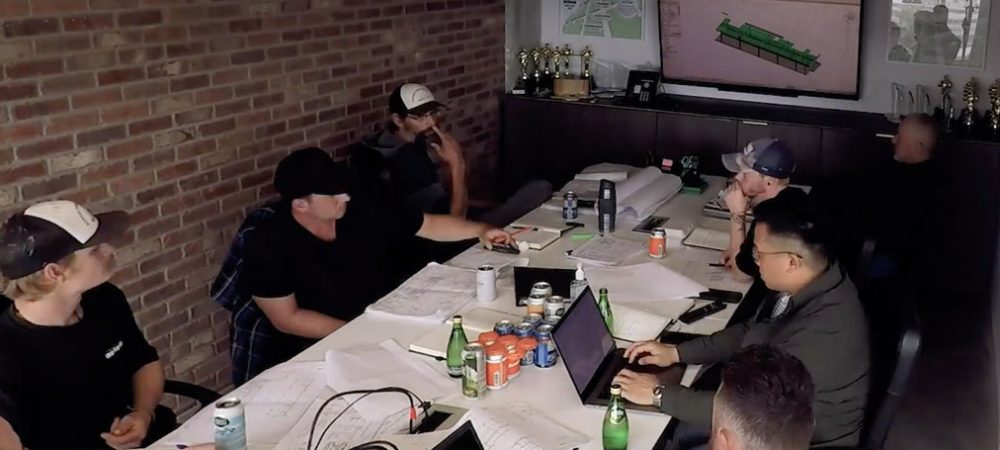
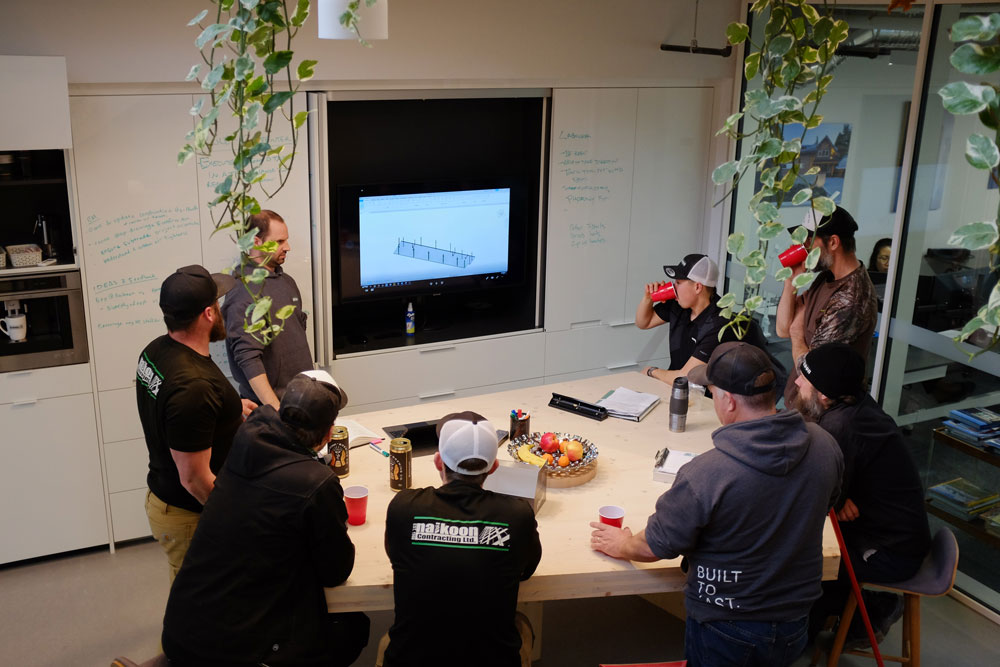
From the boardroom to the off-site yard, we transitioned from the digital model to the real thing. We applied primer and a peel and stick membrane from Soprema to the bare, Structurlam CLT panels. Next up were insulation, clips, and hat tracks. Panel by panel, each went through our ‘flying factory’ ensuring protection from rain and dust.
In preparation for the big install, we fitted and attached all custom-made timber connections to the glulam posts, so that when the time came to transport them they were ready-to-go. Attention to small details, like the order panels are placed on truck, matter to ensure that installation is smooth and efficient.
Check out this video with Construction Manager Lucas, where he explains the logistics prefabrication process of the build.
One of the benefits of a project like 1 Lonsdale is the impact it has on our team. Construction Manager Ryan shares his thoughts on new building concepts and modern ways of working within the industry, such as utilizing renewable resources like mass timber and getting to work with advanced tools and machinery.
With all the planning, prepping, and prefabricating complete, we were feeling confident for a successful construction phase. Below, see how our work comes together in a ten-day install.
We’re thrilled with the outcome of this exciting and challenging installation. We’d like to send a huge thank you to our friends at Eagle West Cranes and to our amazing team who have done a fantastic job so far at this project – go team!
Project team:
Owners: Babco Equities
Architecture: Hemsworth Architecture Inc.
Structural Engineer: Equilibrium Consulting Inc.
Mechanical & Electrical Engineer: MCW Consultants Ltd.
Passive House Consultant: Peel Passive House Consultant Ltd.
Geotechnical Engineer: GVH Consulting Ltd
Landscape: Prospect & Refuge
Code: LMDG
Glulam and CLT supplied by Structurlam.
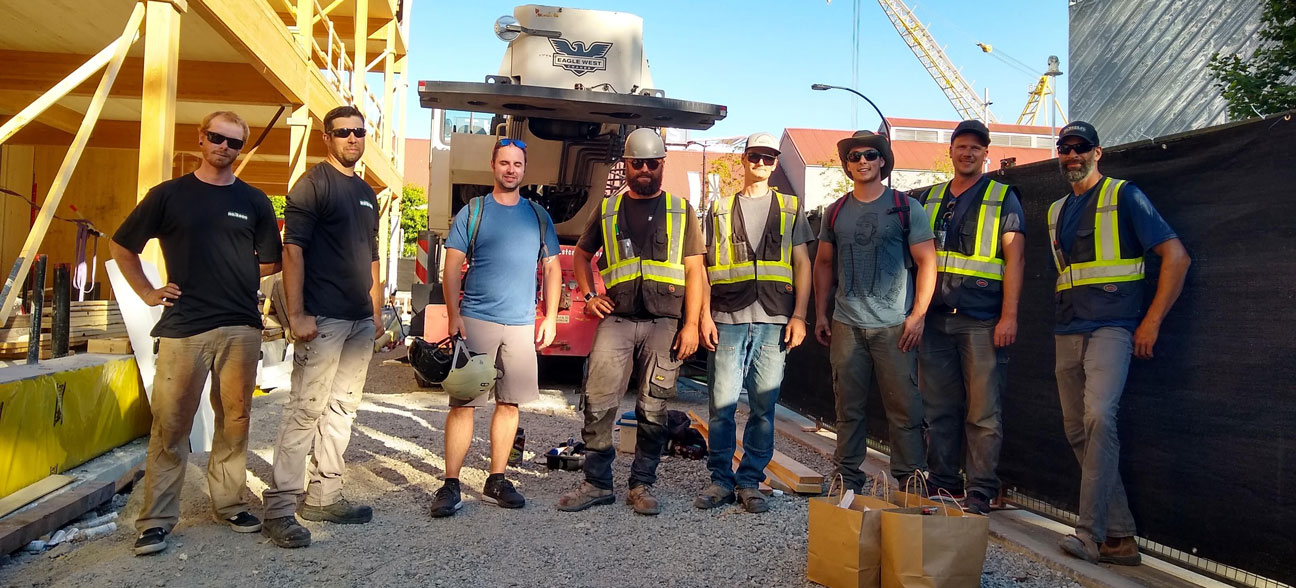